Hydrocracking is a process by which the hydrocarbon molecules of petroleum are broken into simpler molecules, as of gasoline or kerosene, by the addition of hydrogen under high pressure and in the presence of a catalyst. This process employs hydrogen gas to improve the hydrogen-carbon ratio in the cracked molecules and to arrive at a broader range of end products.The major products from hydrocracking are jet fuel and diesel, but low-sulfur naphtha fractions and LPG are also produced.
All these products have a very low content of sulfur and other contaminants. Hydrocracking is a catalytic chemical process used in petroleum refineries for converting the high-boiling hydrocarbons in petroleum to low-boiling products such as gasoline, kerosene, jet fuel and diesel oil. The process takes place in a hydrogen-rich atmosphere at elevated temperatures (500–800 °F, 260–425 °C) and pressures (35–200 bars).Any sulfur and nitrogen present in the hydrocracking feedstock are, to a large extent, also hydrogenated and form gaseous hydrogen sulfide (H 2S) and ammonia (NH 3), which are subsequently removed. The result is that the hydrocracking products are essentially free of sulfur and nitrogen impurities and consist mostly of paraffinic hydrocarbons.Hydrocracking catalysts consist of active metals on solid, acidic supports and have a dual function, specifically a cracking function and a hydrogenation function.
The cracking function is provided by the acid catalyst support and the hydrogenation function is provided by the metals.The hydrocracking process depends on the nature of the feedstock and the relative rates of the two competing reactions.
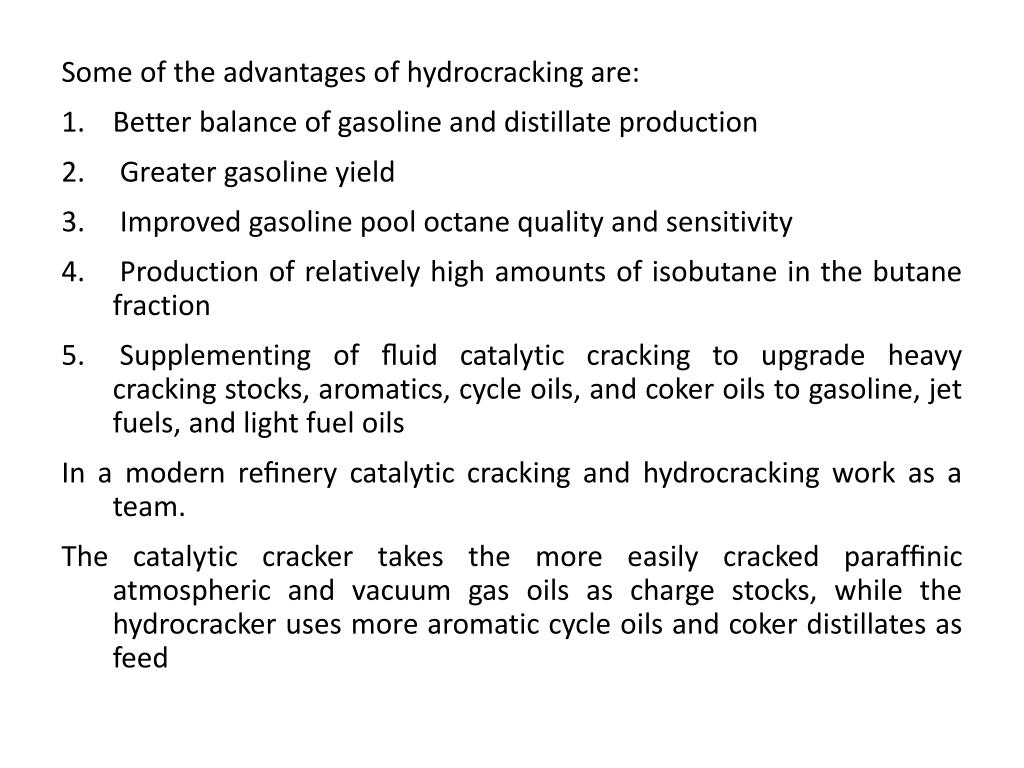

GB 2 104 545 A 1SPECIFICATIONLignin hydrocracking process to produce phenol and benzeneThis invention relates to the catalytic hydrocracking of lignin-containing feedstocks to produce mono-aromatic phenol-containing products. It relates particularly to such a lignin hydrocracking process 5 followed by hydrodealkylation of the mono-aromatic liquid to produce phenol and benzene products. 5Lignin is an aromatic polymer found in all vascular plants. It is currently produced as a co-product of paper pulp and burned for its fuel value. When petroleum feedstock was cheap, lignin was not worth recovering as a chemical feedstock. However, as petroleum feedstocks become scarcer and more expensive, and ever increasing percentage comes from foreign sources, more consideration is being 10 given to using lignin, which is a domestic renewable feedstock, as a source of mono-aromatic products, 10 particularly phenol.Lignin constitutes roughly 25% of lignocellulosic biomass, which includes all vascular plants.Lignin gives plants rigidity and protection and helps regulate the permeation of water.
It is formed within the plant primarily by the dehydrogenative polymerization of three precursors: trans-coniferyl, 15 trans-sinapyl and trans-p-coumaryl alcohol. The relative amounts of each component and their linkages 15 vary with wood types. Trans-coniferyl alcohol is always the major component, and hardwood lignins contain more trans-sinapyl structures.In wood pulping via the kraft process, cellulose, hemi-cellulose and lignin are separated by dissolving hemi-cellulose and lignin in an alkaline sodium sulphate/sulphide solution at elevated 20 temperature and pressure, yielding the so-called black liquor. Wood lignin is considerably changed by 20 kraft cooking. Condensations involving formaldehyde or active beta-carbonyl derivatives lead to methylene-linked aromatic rings and an increase in molecular weight. At the same time, alkaline cleavage of phenolic ethers occurs. As a result of the alkaline cleavage, phenolic hydroxyls increase from 0.3 per monomer in the protolignin to almost 1.0 in the dissolved lignin.25 When sufficiently depolymerized, the lignin phenolate form dissolves in the black liquor.
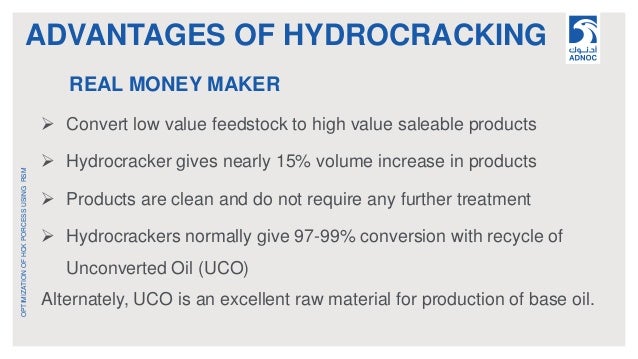
The 25phenolic groups can be liberated by acidification with carbon dioxide obtained from stack gases. This causes the lignin to precipitate, aided by the salting-out effect of the sodium salts of the black liquor.Lignin is filtered at 60—80°C. Further purification by solution in dilute alkali and reprecipitation with sulphuric acid gives a kraft lignin, such as that used as a feedstock in our invention (Table 1). Kraft lignin 30 has a typical average molecular weight of about 3500, which indicates that the average softwood kraft 30 lignin comprises about 20 starting units.2GB 2 104 545 A 2TABLE 1Analysis of Kraft Lignin Charge Stock (W%)Ash by Combustion1.40Water1.02Carbon(organic)64.89Carbon(Na2C03)0.08Hydrogen(ex. H20)5.67Sulphur(Na2S04)0.16Sulphur(organic)1.19Oxygen(Na2C03 + Na2S04)0.64Oxygen(organic sulphur)0.60Oxygen(organic)25.23Sodium(Na2C03 + Na2S04)0.52Organic, W%100.00Carbon64.89Hydrogen5.67Oxygen25.23 95.79U.S.
Patent No, 2,328,749 to Sherrard discloses an early batch-type process for catalytic hydrogenation of wood material to remove lignin and make cellulose. 2,947,739 to Gaslini discloses a process for hydrogenation of ligno-cellulosic materials using a soluble metal carbonyl 5 catalyst under relatively low temperature and pressure conditions. 2,991,314 to Giesen 5 discloses a continuous non-catalytic process for cleavage of lignin to produce phenols at temperatures above 300°C and pressures above 355 bar (350 atm) to yield distillable lignin products. Also,hydrogenation of lignin using the Noguschi batch-type process developed in Japan is disclosed by Goheen in Adv.
Advantages Of Hydrotreating Process
In Chem, Ser. 59,226 (1966).